- BOAT OF THE YEAR
- Newsletters
- Sailboat Reviews
- Boating Safety
- Sails and Rigging
- Maintenance
- Sailing Totem
- Sailor & Galley
- Living Aboard
- Destinations
- Gear & Electronics
- Charter Resources
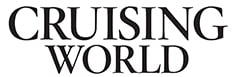

How It’s Made: Fiberglass Hulls
- By Dufour Yachts
- Updated: March 8, 2016
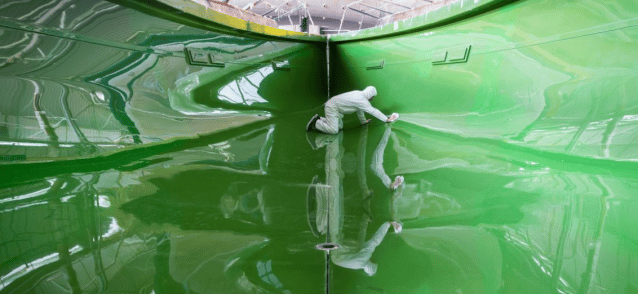
- More: boatbuilding , dufour , fiberglass , how it's made , photos , Sailboats
- More Sailboats

For Sale: 1998 Hinckley 51

Sailboat Review: HH Catamarans HH44

Sailboat Preview: 2 Sportboats We Love

Sailboat Preview: Windelo 50 Yachting

Fatty Goodlander: Where I Fall Short as Skipper

For Yachts or Home, Teak Stands the Test of Time

Shaft Bearing Maintenance Tips

- Digital Edition
- Customer Service
- Privacy Policy
- Email Newsletters
- Cruising World
- Sailing World
- Salt Water Sportsman
- Sport Fishing
- Wakeboarding
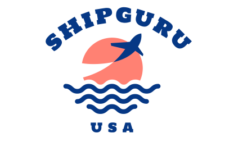
All About Fiberglass: A Boat Builder’s Material Guide

Fiberglass is a versatile and reliable material used in many boat-building projects. It’s lightweight, strong, and can be shaped into virtually any form. It is sturdy and resistant to corrosion, making it a preferred choice for boat builders.
Table of Contents
What is Fiberglass?
Invented in the 1930s, fiberglass is a synthetic material that has revolutionized the marine industry.
Fiberglass is made up of tiny strands of glass that are woven together to create a strong, durable material. The glass is coated in a resin that hardens and cures over time, creating a sturdy composite material that can withstand a lot of wear and tear.
Fiberglass has become a favorite material for boat builders because of its superior qualities and its ability to withstand harsh marine conditions.
The Different Types of Fiberglass
Basically, there are four different types of fiberglass that can be used, each with their own unique characteristics and properties.
1. E-Glass Fiberglass:
This type of fiberglass is the most common and is made from electrical grade glass. E-glass fiberglass has good strength and is highly resistant to chemicals and weathering. It is ideal for use in boat hulls , decks, and other areas that require strength and durability.
2. S-Glass Fiberglass:
S-glass is a higher-strength type of fiberglass that is made from a type of glass called magnesium aluminosilicate. This type of fiberglass is used in high- performance boats and racing yachts, as it is lighter and stronger than E-glass.
3. Kevlar Reinforced Fiberglass:
Kevlar-reinforced fiberglass is made by adding Kevlar fibers to the fiberglass resin. This type of fiberglass is highly resistant to impact and punctures, making it ideal for use in areas that may be subject to damage from rocks, logs, or other objects.
4. Carbon Fiber Reinforced Fiberglass:
Carbon fiber reinforced fiberglass is made by adding carbon fibers to the fiberglass resin . This type of fiberglass is extremely strong and lightweight, making it ideal for use in racing yachts and high-performance boats.
What are the materials used in making fiberglass boat?
Fiberglass and foam core are the two main materials.
In addition to fiberglass, boat builders also use a variety of other materials to strengthen and support the hull and other parts of the boat. One of these materials is a foam core, which is placed between layers of fiberglass to provide added insulation and buoyancy .
Also Read: Boatbuilding Materials: A Comprehensive Guide
How is fiberglass boat built?
Here are the general steps involved in constructing a fiberglass boat:
1. Hull Design and Molds: The boat’s design is first created on paper or computer, then a plug is constructed to create a mold for the fiberglass hull.
2. Applying the Gelcoat: The gel coat is the outer layer of the boat, which protects the fiberglass and gives the boat its color.
3. Laminating the Hull: Layers of fiberglass are then laid over the gel coat, which is then saturated with resin. This process is repeated until the desired thickness is achieved.
4. Curing : Once the laminate is complete, the boat is allowed to cure. The curing process can take anywhere from a few hours to a few days, depending on the size and complexity of the boat.
5. De-molding and Finishing: Once cured, the boat is removed from the mold and any excess material is trimmed away. The boat is then sanded and painted or coated with additional layers of resin for added protection.
6. Fitting and Assembly: Finally, the boat is fitted with any necessary hardware such as electrical and plumbing systems, steering mechanisms, and seating.
Here is a good video to show you step by step on how to build a fiberglass boat
How many layers of fiberglass do you need for a boat hull?
For smaller boats, two to three layers of fiberglass may be sufficient, whereas larger boats may require up to five or more layers.
Each layer of fiberglass adds strength to the hull , and it is important to ensure that each layer is properly bonded to the previous layer.
How thick are fiberglass boat hulls?
Generally, the thickness of a fiberglass boat hull is measured in millimeters, with thicker hulls being stronger and more durable.
For smaller boats like dinghies and kayaks, the hull thickness may only be around 2-3mm. For larger boats, such as sailboats or yachts, the hull thickness may range from 5-10mm or even thicker in certain areas such as the keel or the bow.
Do you sand between coats of fiberglass?
Yes, sanding between coats of fiberglass is important for achieving a smooth and even surface.
Before applying the next coat of fiberglass, it is recommended to sand the previous layer with fine-grit sandpaper. This helps remove any roughness, bumps, or bubbles that may have formed during the previous application.
Sanding also helps the new layer of fiberglass adhere better to the previous layer.
It is important to note that fiberglass dust can be hazardous to health if inhaled, so it is essential to wear a mask and take necessary precautions while sanding.
What grit sandpaper for fiberglass boat?
Depending on the condition of the surface and the task at hand, you can start with grit ranging from 60 to 120.
After the initial sanding, you’ll want to switch to a finer grit sandpaper to smooth out the surface. A grit between 220 and 320 is suitable for this purpose. This step is critical for creating a polished and smooth finish for your fiberglass boat.
It’s also important to use wet sandpaper when working with fiberglass. Wet sandpaper helps to minimize the risk of creating dust particles that can irritate the lungs and eyes.
How often should you wax a fiberglass boat?
Generally, boat owners should wax their fiberglass boats twice a year, once before the season begins and again after the season ends.
Waxing your boat before the season begins will protect it from the sun, saltwater, and other elements that can cause damage to the fiberglass surface.
The wax provides a barrier that repels water, which prevents any potential for osmotic blistering on the hull. The barrier also repels dirt and grime, which keeps your boat looking shiny and new.
After the season ends, it’s important to wax your fiberglass boat to protect it during the off-season.
Waxing after the season helps to remove any dirt or debris that may have accumulated during use and adds an additional layer of protection for storage. It’s especially crucial for boats stored in outdoor facilities or on a lift where it will be exposed to the elements.
How long does it take fiberglass to cure on a boat?
Curing is the process of resin hardening and bonding with the fibers to create a strong, durable hull.
The time it takes for fiberglass to cure can vary depending on a variety of factors, such as temperature, humidity, and the type of resin being used.
In general, however, most fiberglass manufacturers recommend waiting at least 24 hours before continuing work on a fiberglass boat after applying a layer of resin .
How heavy is an 18-foot fiberglass boat?
On average, an 18-foot fiberglass boat will weigh between 1,800 and 2,800 pounds, depending on its construction and features.
However, it’s important to keep in mind that this is just an estimate and that the actual weight can vary depending on a variety of factors.
Is fiberglass expensive?
Generally, the cost of fiberglass can range from $0.50 to $2.00 per square foot. However, this price may go up or down based on several factors such as the thickness and weight of the fiberglass, the type of resin used, and the brand.
On average, a 20–25-foot boat hull made of fiberglass can cost anywhere from $5,000 to $10,000 or more,
Pros and Cons of fiberglass
Fiberglass is a popular boat-building material for good reason, but it’s not without its drawbacks. Let’s take a look at some of the pros and cons of using fiberglass in boat construction.
- Fiberglass is incredibly durable and long-lasting. With proper maintenance, a fiberglass boat can last for decades.
- It’s also lightweight, which can lead to improved fuel efficiency and easier handling.
- Fiberglass boats are relatively easy to repair compared to other materials like wood or aluminum.
- It’s also a versatile material that can be used to create complex shapes and designs.
- Fiberglass can be more expensive than other materials like aluminum or wood.
- It’s also not as eco-friendly, as it requires petroleum-based products in its construction.
- While it’s relatively easy to repair, it can still be time-consuming and costly compared to other materials.
- Fiberglass can also be prone to cracking and blistering if not maintained properly.
How long do fiberglass hulls last?
With proper maintenance , a fiberglass hull can last for decades. In fact, many fiberglass boats from the 1970s and 1980s are still in use today.

- 2024 BOAT BUYERS GUIDE
- Email Newsletters
- Boat of the Year
- 2024 Freshwater Boat and Gear Buyers Guide
- 2024 Boat Buyers Guide
- 2024 Water Sports Boat Buyers Guide
- 2024 Pontoon Boat Buyers Guide
- Cruising Boats
- Pontoon Boats
- Fishing Boats
- Personal Watercraft
- Water Sports
- Boat Walkthroughs
- What To Look For
- Watersports Favorites Spring 2022
- Boating Lab
- Boating Safety
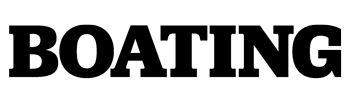
Boat Construction Comparison
- By Rick Strand
- Updated: September 11, 2013
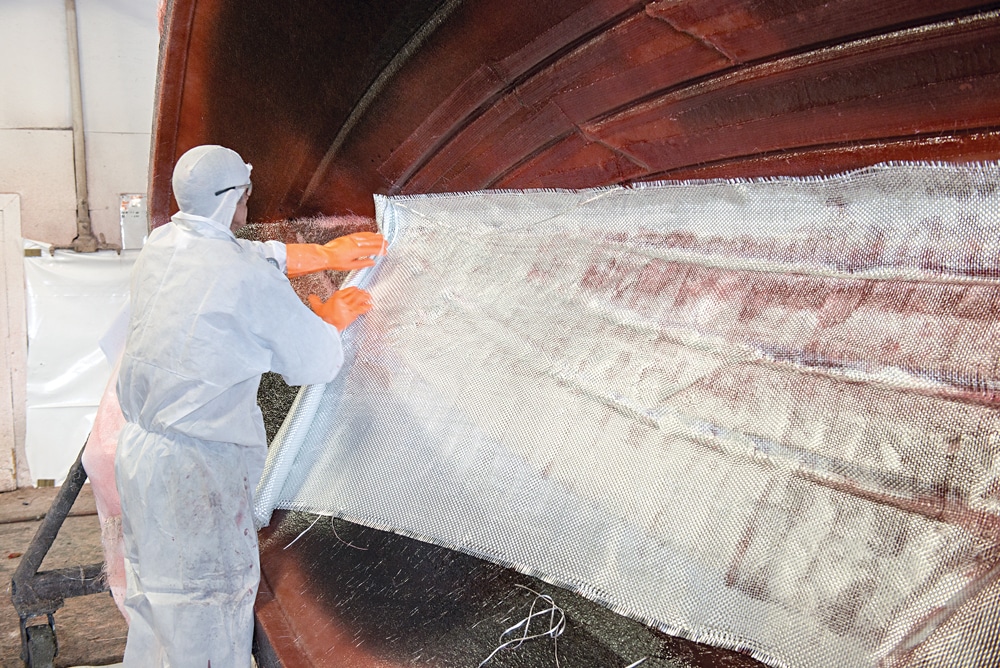
Engineer and composites expert Rick Strand is president at Impact Matrix Systems, Hampstead, New Hampshire. He has worked for Boston Whaler, ITW Plexus and TPI Composites abd consulted for Baja, Sea Ray and others.
We take it that you know the basics, such as fiber provides the strength and resin provides the stiffness in a fiberglass laminate. And that composite is just a fancy term for a structure made from a combination of materials (hey, straw and clay bricks are “composite”). But can you sift through the rest of the jabber at a boat show?
The materials used to construct boats are varied in cost, application and how they perform. This primer is intended to help you sort the truth from the marketing mush and sales hype.
Fibers Most boat hulls are made using either knitted or woven fabric created from glass fibers. In some fabrics, the fibers crisscross at 0- and 90-degree orientations (0/90). Other axial configurations include plus and minus 45 degrees and either 0 degrees or 90 degrees. The directionality of the fibers enables the engineer to orient them in the direction of the stresses applied to the hull at any location. So, the use of “0” or “+/- 45-degree” fiber doesn’t make a boat better; it simply designates the application.
Woven fabrics require simpler machinery to produce and are hence less expensive than knitted fabric reinforcements. With knits, fibers are laid flat on a surface (by machine) and are knitted through with a lightweight and tenacious fiber to hold them together. The fibers in knitted fabric lie almost absolutely flat.
Woven fabrics’ fiber bundles run over and under each other creating a bulkier material. As a result, there are several things to consider about a boat using woven fabric. First, as the hull ages in the sun, it can develop “print-through.” This condition manifests itself by visibly transmitting the fiber so that the finish is no longer smooth but appears slightly distorted in a crisscross pattern. This occurs because the resins in the hull composite shrink after sitting in the hot sun. This condition is seen in darker-color hulls (green, blue and black) more often because they can reach temperatures of more than 200 degrees F in the direct summer sun. White hulls may get to only 160 F because they reflect more of the sun’s rays. In addition, the dark, shiny colors show the condition more than a light color does because of the way they reflect light. Knitted fibers lie flat, have lower shrinkage stresses and will not produce the print-through condition.
From a structural standpoint, builders that utilize knitted fabric as their primary reinforcement will make hulls, decks and parts that are stronger and stiffer (given proper engineering) than those built with woven-fabric composites. The parts will also be lighter. For the same reason that columns supporting buildings are straight and not wavy, knitted fibers more effectively line up in the direction of applied forces while woven fibers line up like springs. They have less strength and stiffness when they are “off-axis” to the forces. In addition, woven fibers have wells of empty space between the weave that need to be filled with resin to produce the composite. Knitted fabrics have less of this space. Therefore, woven fabrics require more resin to wet out in production. The result is heavier, more structurally inefficient composites.
Finally, woven fabrics will last a shorter period of time before the composites break down and will fatigue from repeated stress (pounding and slamming) on the out-of-plane fibers (springs) formed by the weave. At the end of the day, a boat utilizing knitted fabrics and an equivalent structural design would last longer and experience less cracking. This is particularly useful in deck composites and internal components having odd or transitional shapes.
Backup Materials From engines to cleats the problems that create the most headaches for owners are those associated with backing up hardware. There’s no reason to buy a new boat using plywood in the stringers or floor, as backups for cleats, in handrails, around hatches and, most of all, in the transom. In my many years of marine experience, I’ve learned that doing so will have you removing what little hair you may have left.
Plywood will get wet and rot. You will never be able to sink another new screw into it. Your transom will need to be replaced eventually and so will your stringers, toe rails, etc., etc. Don’t buy into it. Today, there are numerous alternative materials referred to as “boards” that are designed, engineered and produced for this purpose. If they get wet, they will not rot or lose properties. They will last longer and make your life easier as an owner. Many quality boats used plywood for many years because it was cheap, available and easy to cut and fit. Today, there is no excuse for it. Make sure a polymer backer board is used in your vessel. You will enjoy boating all the more for it. The risk of increased costs and lost time on the water associated with using plywood in a new fiberglass boat are far too high to buy one using them.
Resins The resin used to build your boat holds everything together. Polyester resins are popular, but polyester is a generic term covering a vast array of brands and types, differentiated in both name and performance by the type of acid used to make each one. Those acids are orthophthalic, isophthalic and terephthalic. Orthophthalic acid is used to produce general-purpose marine resins. Isophthalic acid is used to produce a more chemical-resistant and slightly stronger grade. Terephthalic acid is not common in boats.
You’ll also hear “DCPD modified resin” bandied about. Without getting overly complicated, DCPD (dicyclopentadiene) is a big molecule. Within a polyester resin chain is the ester linkage — like a repeating linkage in a long chain. This linkage is a chemical bond that can be attacked by water over the long term. Eventually water can break this bond, starting a long-term degradation process that can lead to blistering or even your bottom cracking open. DCPD shields against water, rendering the ester linkage more stable in a wet environment. It also reduces the cost of the resin. Its downfall is its brittleness. It can reduce the crack resistance of your boat.
Also in this category are the vinylester resins. They are more expensive but do not have the ester linkage. Instead, they have an ether linkage, a more moisture-stable connector in the molecule. These resins have great chemical and moisture resistance. They are also much tougher and more flexible than the others. This means that design stress levels can be higher in the composites. This equates to a lighter, more durable boat that can take a beating and keep on ticking without cracking or breaking. Vinylesters are what gave us a revolution back in the early ’80s, when builders could begin to produce hulls that would not blister. Blistering, as you recall, is an indirect result of the ester linkages breaking in the presence of water. Therefore, vinylester resins are the resin of choice for the seeker of a trouble-free experience. You should make sure that your boat is produced with them if the boatbuilder works with polyester resins.
Epoxies are in a similar realm to vinylesters when it comes to performance in a marine composite, though you won’t find many production boats using it. It’s more fickle to use and more sensitive to heat, and some workers are allergic to it. However, if a custom boat is what you seek, it’s a fine alternative. And improvements in chemistry have helped overcome its manufacturing problems.
Generally, the higher-tech and lighter the construction, the more likely you are to find an epoxy choice in resin systems. Vinylester resin is the more likely to be used in a modern marine composite associated with a quality production-boat builder.
The most important consideration concerning all of the materials discussed is the quality of competence of the builders. This has been the biggest ball and chain ever dragged by the industry. Builders who do not have a quality manual probably don’t have a program, and if they don’t have a program (and I mean a good one), you will not have a trouble-free experience. Take it from someone who has done many a quality audit: It does not matter how good the materials are that you are buying. If you do not use them correctly and make sure that is the case every day, you cannot build a trouble-free boat. I do mean trouble-free for years. These days, the industry leaders are doing pretty well here. Many others still are not. The structural “guts” aspects of today’s boats are fairly good and well understood. All the other systems on a boat will need to be dealt with next. When that happens, your boat will be a lot like your car. It will be predictable, reliable and somewhat trouble-free.
Beyond Glass Fiber Carbon fibers and aramid fibers are lighter than glass fibers and, in many configurations, stiffer and stronger too. But they don’t come cheap. Today, glass fiber may cost between $1.50 and $2.50 per pound, while carbon fibers may run in the pricier $18 to $26 per pound range.
Carbon has found strong application in boatbuilding, where aramid (such as Kevlar by DuPont) has been largely withdrawn from the marine market. This is partially because aramid fiber does not adhere well to most resins. Also, it has great tensile strength in the direction of the fiber, but it suffers when loaded off-axis at most angles to the fiber, as well as in compression.
A new technology about to make it to market could drastically improve these problems. This newer technology bonds fibers into a flat configuration that maximizes strength as well as the amount of fiber per unit thickness (in other words, heavier amounts of fiber in a thinner product). This allows lower resin use and lighter-weight construction. For the boat buyer, this can mean a faster and/or more fuel-efficient boat.
Learn More About Cored Composite Boat Structures
Talk about an area of contention over the years…core materials are it. Cores, including foams and balsa wood, are good materials. It is the way they are installed that can make them an owner’s nightmare. Today, improvements in closed molding techniques, like resin infusion, have bettered the quality of core installation. In the hand-laid days, a good installation was like pinning the tail on the donkey. Builders were blindfolded because they couldn’t see the “downside” of the core. The vacuum infusion process has improved core installations, performance and longevity. Both balsa and foam cores can be well produced and last for years. In terms of performance, a cored or sandwich composite is better than a solid composite with respect to strength-to-weight ratio. Cored composites yield lighter, faster and more fuel-efficient boats.
Do not be afraid of buying a new boat made with core materials, but do your homework in selecting your brand and what is behind it. And, FYI, most of those windmill blades you see spinning on the distant peaks are built using vacuum infusion with cored composites.
- More: Boats , How-To , Used Boats

The Perks of Portable Electric Outboards

Choosing the Right Pipework Finish

Pleasurecraft Marine’s New ZZ8R and ZZ8S Engines

Mercury Marine Intros MerCruiser T8200 Tow Sport Inboard

Sea Ray SPX 190: Sporty Versatility on the Water
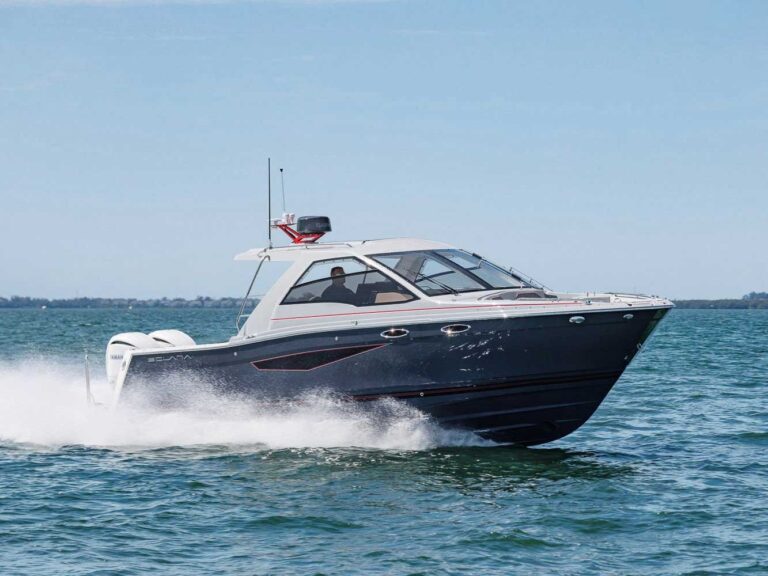
2024 Solara S-310 SC

Airmar Medium Ultra-Wide-Beam Transducers
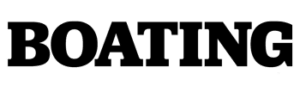
- Digital Edition
- Customer Service
- Privacy Policy
- Cruising World
- Sailing World
- Salt Water Sportsman
- Sport Fishing
- Wakeboarding
Many products featured on this site were editorially chosen. Boating may receive financial compensation for products purchased through this site.
Copyright © 2024 Boating Firecrown . All rights reserved. Reproduction in whole or in part without permission is prohibited.

How to Build a Fiberglass Boat: The Ultimate Guide
Are you interested in learning how to build a fiberglass boat? If so, you have come to the right place! In this blog post, we will walk you through the process step-by-step. Building a fiberglass boat can be a challenging but rewarding experience. With the right tools and instructions, you can easily create your own boat without spending a fortune.
Choose the right boat plans
Gather the necessary materials, assemble the frame of the boat, install the deck and cabin, add the finishing touches, take your new boat for a test drive, what are the benefits of fiberglass boats, are fiberglass boats difficult to build, how long does it take to build a fiberglass boat, what is the estimated cost of building a fiberglass boat.
Building your own boat can be a rewarding experience, but it’s important to choose the right plans. If you’re planning to build a fiberglass boat, you’ll need to find plans that are specifically designed for that material. Fiberglass is a tough and durable material, but it requires special techniques to work with.
Choosing the wrong plans could result in a lot of wasted time and effort, so it’s important to do your research before you get started. The good news is that there are plenty of resources available online, so you should be able to find everything you need to get started.
With a little bit of planning and the right set of plans, you can build the fiberglass boat of your dreams.
Building a fiberglass boat can be a rewarding experience, but it’s important to have the right materials on hand before getting started. Fiberglass cloth is the primary material used in constructing the hull of a fiberglass boat. This cloth is available in different weights and sizes, so it’s important to choose the right one for your project.
In addition to fiberglass cloth, you’ll also need a resin system designed specifically for use with fiberglass. This resin will provide the necessary strength and durability to your finished boat.
Finally, you’ll need some type of mold or form to shape the hull of your boat as it dries. With the right materials on hand, you’ll be well on your way to building a high-quality fiberglass boat.
One of the most important steps is assembling the frame. This can be done by attaching the hull to the keel and then adding the stringers. The hull provides the shape of the boat, while the keel and stringers add strength and rigidity.
Once the frame is complete, it can be covered with fiberglass cloth and resin to create a durable and watertight hull. With careful planning and attention to detail, it is possible to build a beautiful and seaworthy fiberglass boat.
Installing a deck and cabin in your fiberglass boat will add both beauty and function. The deck will provide a stable, level surface on which to move about, while the cabin will offer protection from the elements and a place to store gear. Both can be easily installed with a few common tools.
First, mark the desired location of the deck or cabin on the hull of the boat. Then, using a drill, create holes for mounting screws.
Next, position the deck or cabin in place and screw it into the hull.
Finally, seal any gaps with silicone caulk to ensure a watertight seal. With a little effort, you can transform your boat into a comfortable and stylish vessel.
After you have finished fiberglassing your boat, there are still a few things you need to do in order to make it look its best. Here are some tips for adding the finishing touches to your fiberglass boat:
- Start by sanding the hull with medium-grit sandpaper. This will smooth out any imperfections and prepare the surface for painting.
- Next, apply a primer coat followed by a top coat of paint. Be sure to use marine-grade paint that is specially formulated for use on boats.
- Finally, add any decals or other graphics that you want to use to personalize your boat. You can find a wide variety of boat graphics online or at your local boating store.
By following these simple steps, you can ensure that your fiberglass boat looks great for years to come.
After adding the finishing touches to your fiberglass boat, there’s only one thing left to do: take it for a test drive! Whether you’re testing the waters for the first time or taking your vessel out for a joyride, there are a few things to keep in mind.
First, be sure to inspect your boat thoroughly before setting out. This includes checking the hull for any cracks or leaks, as well as making sure all of your equipment is in good working order.
Once you’re on the water, pay attention to how your boat handles. Does it feel stable? Are you able to easily steer it in the direction you want to go? If not, make some adjustments and try again. With a little practice, you’ll be sailing smoothly in no time.

Fiberglass boats have a number of advantages over traditional wooden boats. They are lighter in weight, making them easier to handle and less likely to capsize. They are also more durable, and resistant to rot, UV radiation, and impacts. In addition, fiberglass boats are easier to repair than wooden boats, and they often have a sleeker, more modern appearance.
As a result, fiberglass boats have become increasingly popular in recent years. Whether you’re looking for a fishing boat, a pleasure boat, or a racing boat, chances are there’s a fiberglass model that will suit your needs.
It’s no secret that fiberglass boats are among the most popular types of vessels on the water. Thanks to their durability and low maintenance, they offer owners years of trouble-free use. But what many people don’t realize is that fiberglass boats can also be quite easy to build.
Unlike wooden boats, which require extensive carpentry skills, fiberglass vessels can be constructed using simple tools and materials. The hulls of most fiberglass boats are made by layering sheets of fiberglass matting, which is then held together with resin. The deck and other structural components are added last.
As long as you take care to follow the instructions, building a fiberglass boat can be a relatively simple process.
The answer to this question depends on a number of factors, including the size and type of boat being built. Generally speaking, it takes significantly less time to build a fiberglass boat than it does to build a wooden one. This is because fiberglass is a much lighter material, and it can be molded into shape more easily.
As a result, fiberglass boats can often be assembled in a matter of weeks, whereas wooden boats can take months or even years to construct. Of course, the time required to build a boat also depends on the experience and skill of the builder.
An experienced shipwright will be able to build a boat more quickly than someone with no experience. In short, there is no definitive answer to the question of how long it takes to build a fiberglass boat. The time required will vary depending on the individual circumstances.
The cost of building a fiberglass boat depends on a number of factors, including the size and complexity of the boat, the materials used, and the labor required. In general, smaller and simpler boats will be less expensive to build than larger and more complicated ones.
The type of fiberglass used is also a major factor in the cost of construction. For example, boats made with woven fiberglass are typically more expensive than those made with chopped strand mat.
Labor costs can also vary widely, depending on the experience and expertise of the workers involved. In general, it is possible to build a small fiberglass boat for around $3,000-$4,000. Larger and more complex boats can cost upwards of $10,000 or more.
Building a fiberglass boat can be a rewarding experience. It is important to remember, however, that the cost and difficulty of the project will vary depending on the size and complexity of the boat being built. With careful planning and execution, however, anyone can build a beautiful and functional fiberglass boat.
1 thought on “How to Build a Fiberglass Boat: The Ultimate Guide”
i really want to build my own boat that suit my type and would take the opportunity to do a practical task with fiber glassing. so the material you provide in the reading is very valuable and one thing to ask is the items to order from if you could provide a link
thanks and looking forward to hear more on fiber glassing
Leave a Comment Cancel Reply
Your email address will not be published. Required fields are marked *
Save my name, email, and website in this browser for the next time I comment.
Get your Boat Building Free Guide


- ON THE HORIZON
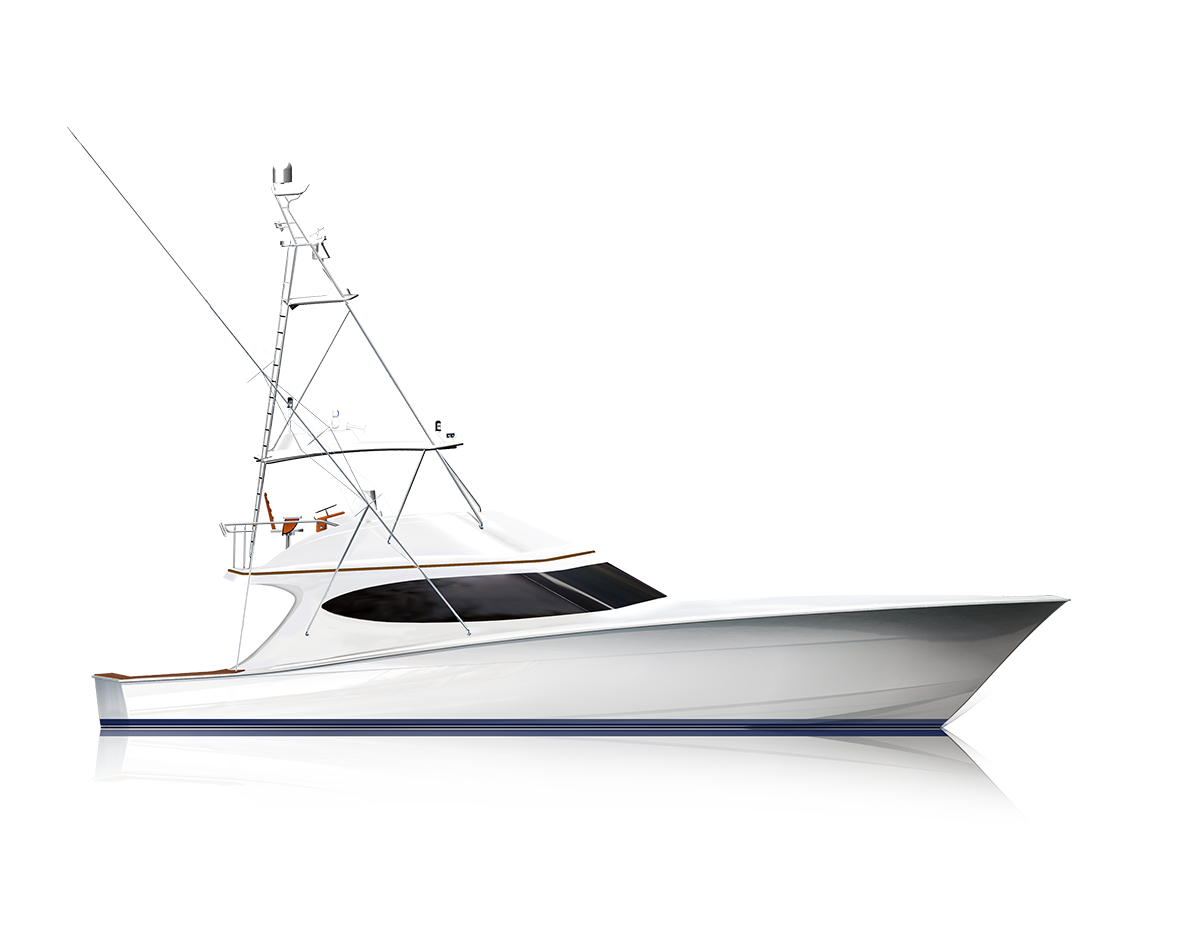
GT 65 Carolina
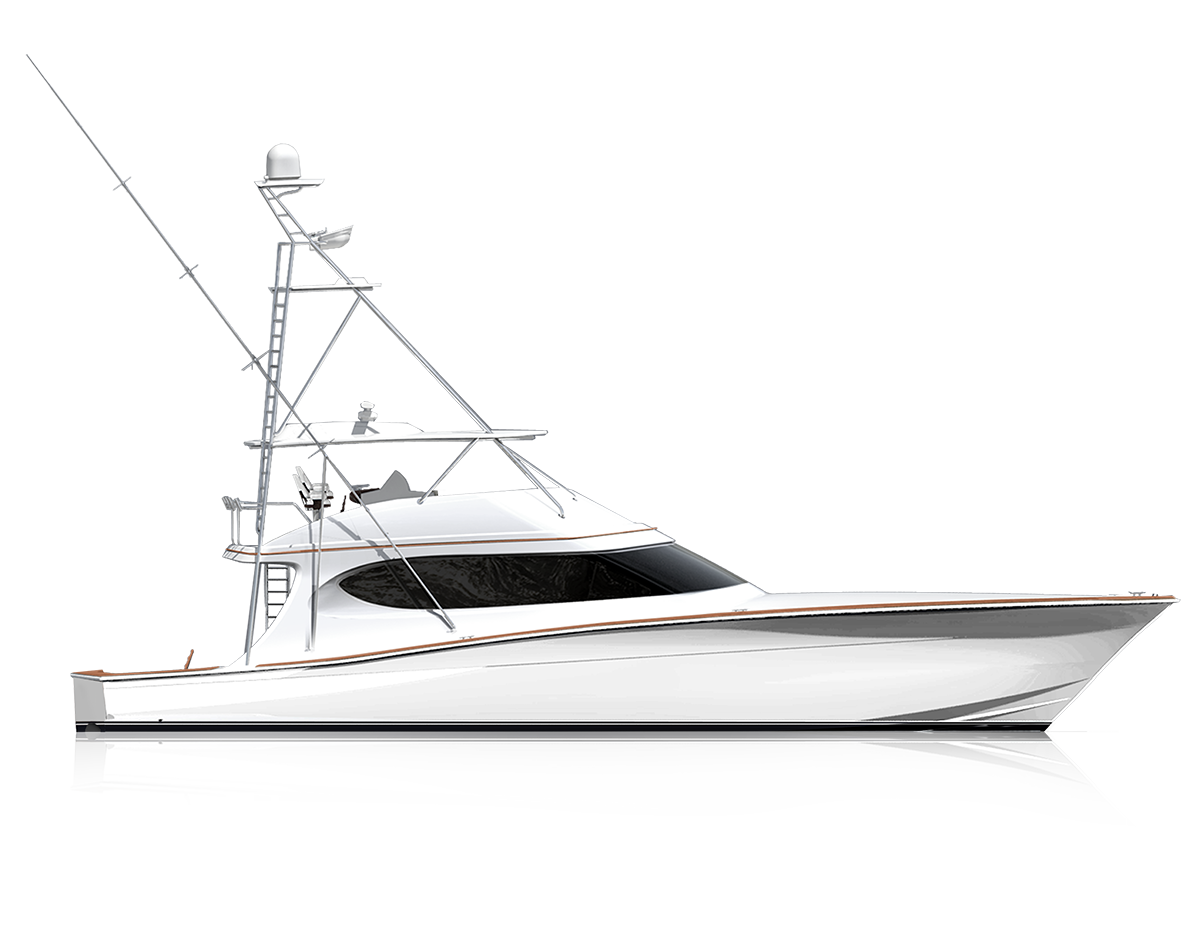
The Hatteras Advantage: Superior Hull Construction
You want to be out where the fish are biting, even when it’s too rough for the other boats to leave the dock. That’s why every Hatteras hull is designed and built to give you a smooth, stable ride in turbulent offshore conditions.
COMPOSITE CONSTRUCTION
Our hulls are built tough, utilizing the highest quality fiberglass and vinylester resin for optimal strength, stiffness and durability. What’s more, during construction we add a full coat of high-performance vinylester gelcoat to each hull mold below the waterline, in order to maximize the hull’s resistance to bottom blisters—something most of our competitors don’t do. Then, we give the hull bottom an additional coat of epoxy resin for added blister protection as part of the anti-fouling system.
THE HATTERAS ADVANTAGE
"A lot of builders put vinylester in their skin coat, but almost no one besides Hatteras uses a vinylester gel coat below the waterline,” said Bob Arthur, Hatteras Yachts manager of structural and composites engineering.
Instead of vacuum-bagging the whole hull, which some builders do in order to remove excess resin from the lay-up quickly, Hatteras uses proprietary vinylester resin infusion technology to make its hulls lighter, stiffer and stronger. The process involves using the vacuum to carefully to pull the vinylester resin through the fiberglass part. “We would rather do infusion and get the cleaner, clearer hull surface it produces than to use vacuum-bagging,” said Arthur. “The infusion allows us to really dial in our resin-to-glass ratio for stiffness and strength.”
Arthur is a 43-year veteran of the Hatteras Yachts team. “What a lot of people don’t know is that back in the ’80s, Hatteras actually helped to develop the very first vinylester gel coat for use in composite construction,” he said. Since 1959, when Hatteras Yachts Founder Willis Slane launched the first boat under 30 feet built of fiberglass rather than wood with the goal of conquering the stormy seas off the North Carolina coast, we’ve been at the leading edge of advanced hull construction.
“I love the product we build, and that it’s known throughout the industry for its beauty and toughness,” said Arthur.
READY FOR MORE?
110 North Glenburnie Road New Bern, NC 28560
SPORTFISH YACHTS
- On The Horizon
- Legacy GT Series
- Request Consultation
- Gear & Apparel
Did You Know That We Offer Contract to Closing Services? Click Here to Find Out More.
Need Marine Financing? Apply Here With Our Partner, First Approval Source
- Catamaran Interviews
- Catamaran Reviews
- Buying Advice
- Selling Advice
- Woods Design Advice
- Admiral 38
- Admiral 40
- Admiral 50
- African Cats
- Fastcat 445
- Americat 3014
- Antares 44
- Aquila 44
- Aventura 37
- Balance 526
- Bali 4.0
- Bali 4.1
- Bali 4.2
- Bali 4.3
- Bali 4.4
- Bali 4.5
- Bali 4.6
- Bali 4.8
- Bali 40 Catspace
- Bali 5.4
- Bali Catsmart
- Beneteau Blue II
- Broadblue 346
- Broadblue 38 Prestige
- Broadblue 385
- Broadblue 435
- Broadblue 46
- Rapier 400
- Rapier 550
- Catalac 10M
- Catalac 11M
- Catalac 12M
- Catalac 8M
- Catalac 900
- Catalac 9M
- Catana 381
- Catana 39
- Catana 401
- Catana 40S
- Catana 411
- Catana 42
- Catana 42 S
- Catana 431
- Catana 44
- Catana 471
- Catana 50
- Catana 521
- Catana 531
- Catana 55
- Catana 581
- Catana 65
- Catathai 44
- Chris White
- Chris White 48 Voyager
- Chris White 55
- Condor 40
- Contour 34
- Corsair F28 R
- De Villiers
- Dean 365
- Dean 400
- Dean 440
- Dean 500
- Dix DH550
- Dolphin 380
- Dolphin 460
- Edel 35
- Endeavour 30
- Endeavour 35 Victory
- Endeavour 36
- Endeavour 44
- Endeavour 44 TrawlerCat
- Endeavour 50 Pilothouse Trawler
- Excess 11
- F-41
- Fisher 28
- Fisher 32
- Fortuna 36 Island Spirit
- Fortuna 401 Island Spirit
- Fountaine Pajot
- FP 32 Maldives
- FP 35 Tobago
- FP 36 Mahe
- FP 37 Antigua
- FP 38 Athena
- FP 39 Fidji
- FP 40 Isla
- FP 40 Lavezzi
- FP 40 Lucia
- FP 40 MY
- FP 40 Summerland MY
- FP 41 Lipari
- FP 42 Astrea
- FP 42 Venezia
- FP 43 Belize
- FP 44 Helia
- FP 44 Orana
- FP 45 Elba
- FP 46 Bahia
- FP 46 Casamance
- FP 48 Salina
- FP 50 Saba
- FP 56 Marquises
- FP 57 Sanya
- FP 58 Ipanema
- FP 60 Eleuthera
- FP Saona 47
- Fusion 40
- Gemini 105
- Gemini 3000
- Gemini 3200
- Gemini 3400
- Gemini Freestyle 37
- Gemini Freestyle 399 Power
- Gemini Legacy 35
- Grainger 420 Mystery Cove
- Gunboat 55
- Hirondelle 7M
- Island Packet
- Island Packet Cat 35
- Kennex 420
- Knysna 440
- Knysna 480
- Knysna 500
- Knysna 550
- Lagoon 35
- Lagoon 37 TPI
- Lagoon 380
- Lagoon 39
- Lagoon 40
- Lagoon 400
- Lagoon 410
- Lagoon 42
- Lagoon 42 TPI
- Lagoon 420
- Lagoon 421
- Lagoon 43 PC
- Lagoon 44 Power Cat
- Lagoon 440
- Lagoon 450
- Lagoon 46
- Lagoon 470
- Lagoon 50
- Lagoon 500
- Lagoon 52F
- Lagoon 55
- Lagoon 560
- Lagoon 570
- Lagoon 620
- Lagoon Seventy 8
- Leeuwin 42
- Leopard 38
- Leopard 39
- Leopard 39 PowerCat
- Leopard 40
- Leopard 42
- Leopard 43
- Leopard 44
- Leopard 45
- Leopard 45 Classic
- Leopard 46
- Leopard 46 Lion PowerCat
- Leopard 47
- Leopard 47 PowerCat
- Leopard 48
- Leopard 50
- Leopard 51 PowerCat
- Leopard 53 PowerCat
- Leopard 58
- Lidgard 73 Executive
- Looping 50
- Maine Cat 30
- Maine Cat 38
- Maine Cat 41
- Manta 40
- Manta 42
- Matrix 450 Vision
- Matrix 760 Silhouette
- Maverick 400
- Maverick 420
- Maverick 440
- Moxie 61
- Nautitech 40
- Nautitech 40 Open
- Nautitech 44 Open
- Nautitech 442
- Nautitech 46 Open
- Nautitech 47
- Nautitech 47 Power
- Nautitech 65
- Neel 45
- Oceanlake Marine AB
- Seacart 30
- Outremer 40
- Outremer 45
- Outremer 50 Standard
- Outremer 55
- Outremer 5X
- PDQ 32
- PDQ 36
- Privilege 37
- Privilege 39
- Privilege 42
- Privilege 43
- Privilege 435
- Privilege 45
- Privilege 465
- Privilege 48 Transcat
- Privilege 482
- Privilege 495
- Privilege 510
- Privilege 65
- Privilege Serie 5
- Prout 31 Quest
- Prout 33 Quest
- Prout 34 Event
- Prout 35 Snowgoose
- Prout 37 Snowgoose
- Prout 37 Snowgoose Elite
- Prout 38
- Prout 38 Manta
- Prout 39 Escale
- Prout 45
- Prout 46
- Robertson and Caine
- Royal Cape 45
- Royal Cape 500 Majestic
- Royal Cape 530 Majestic
- Sailcraft 30 Iroquois
- Sailcraft 32 Comanche
- Sailcraft 35 Cherokee
- Sailcraft 41 Apache
- Sailcraft 44 Apache
- Scape 39
- Wildcat 350
- Seawind 1000
- Seawind 1160
- Seawind 1200
- Seawind 1260
- Seawind 1600
- Simpson 48
- Solaris 36 Sunrise
- Solaris 36 Sunstar
- Solaris 42
- St Francis 44
- St Francis 48
- St Francis 50
- Stealth 11.8
- Sunreef 60
- Sunreef 62
- Sunreef 70
- Sunreef 74C
- Sunreef 82 DD
- Sunreef 88 DD
- Switch 51
- Switch 55
- TRT 1200
- Heavenly Twins 26
- Ocean Twins 38
- Vaan R5
- Vision 444
- Voyage 380 Maxim
- Voyage 400 Norseman
- Voyage 430 Norseman
- Voyage 440
- Voyage 450 Cabriolet
- Voyage 47 Mayotte
- Voyage 480
- Voyage 500
- Voyage 580
- Voyage 590
- Kronos 45
- Wharram 38 Tiki
- AMI 320 Renaissance
- Woods 22 Wizard
- Woods 35 Banshee
- Woods 35 Flica
- Woods 36 Scylla
- Woods 36 Vardo
- Woods 38 Transit
- Woods 40 Meander
- Xquisite X5
- Xquisite X5+
Catamaran Construction – Hulls, Laminates, and Composites
- Post author By BJ Porter
- Post date October 15, 2020
- 4 Comments on Catamaran Construction – Hulls, Laminates, and Composites

It’s a given that catamarans are more sensitive to weight and loading than monohulls. Catamaran builders strive to build the lightest boats they can without sacrificing strength and stiffness, and have adapted new building techniques and materials to meet this target. Cutting weight allows more passengers and gear without sacrificing performance.
And the marketing materials reflect it–they load every review and website with polysyllabic technical jargon describing the design and production choices each builder made to deliver the best boat they can.

But when you’re reading a brochure and you come across phrases like “ hand laid bidirectional GRP ” or “ vacuumed bagged e-glass with vinylester resin over a Divinycell core ” do you know what that really means?
All modern production catamarans are made with “FRP” construction (for Fiber Reinforced Polymer). Composites aren’t new–it’s just using materials together to strengthen the whole assembly. Straw was added to bricks centuries ago, and steel reinforced concrete is a staple of construction over the last century. For boats, it’s the use of stranded fibers and cured resins which make FRP different.
The term “FRP” doesn’t get into the technical detail of which fibers and which plastics, and how they’re put together to build your hull. There’s a wide variety of fiber types which can be stranded, woven, chopped or sprayed in a varied of patterns then combined with several types of resins to make hulls with different characteristics.
Some FRP techniques produce lighter, stronger shapes, while others are quicker to build and less expensive to produce. The choice of technique is a function of many factors, from the number of hulls and parts to be built, the type of parts, the budget for the project, and many design specific requirements for weight and strength.
1. FRP Basics
The principle behind all FRP construction is the same – you lay our fibers in the shape you need, then saturate them with resin, removing all the air and voids you can. Resin is left to cure, then the piece is ready to finish and use.

The reality is more complex, since building a boat isn’t like making a flat board or a simple door. You’ve got a complex shape with a designed set of curves to build. “Tooling” is the set of shapes to make the boat parts; molds to cover with fiberglass to get the right shapes.
That’s what makes FRP so effective – you can make almost anything out of it. But to do so requires a lot of choices about what you need for the project at hand.
There isn’t a “best” all around material or technique choice for all jobs, and sometimes a lower cost technique or easier to work with material may be the better solution to the problem.
A. Fiber types
Fiber choices in the last few decades have expanded past the glass fibers used in the first mass produced boats in the 1960s. FRP construction wasn’t new even then, they built the first composite boats using modern fiberglass in the 1940s.
The major fibers used in marine construction fall into three categories – glass, aramids, and carbon. The primary differences are in the strength to weight ratios of the fibers, durability, elasticity, and cost. Some construction may use blends of fiber types to combine performance characteristics.
Glass – the most common material still, because of its low cost and versatility. The most common variety used in GRP (Glass Reinforced Polymer) is “E-glass” which refers to its strand size and mineral content. Other grades have different and sometimes better mechanical properties, but may be more expensive and less appropriate for boat building use. Fiber sizes run 10 to 25 microns for E-glass, though other grades may be smaller.

Brands like Leopard, Lagoon, and most higher production volume builders use E-glass.
Aramids – this includes brand names like Kevlar, Technora and Twaron. They have higher tensile strength than E-glass, and resistant abrasion and punctures. Kevlar is a common choice for bullet proof body armor, and can built a tough, lightweight hull. The materials can be difficult to work with, as it is very tough to cut the cloth. It is often blended with carbon fiber or other materials – Catana is known for using Twaron blends in hull construction.

Carbon – the ultimate in lightweight, strong construction material. Carbon fiber is the most expensive fiber, and is available in a variety of weights, grades and strengths. Fibers are smaller than glass – down to 5 Micron.
The lightest, most expensive hulls are made from carbon, but a catamaran builder may use carbon in places other than the hull to add strength and stiffness. Carbon boards, rudders, and reinforcing structures can enhance performance without driving the price of the boat beyond reach. Carbon is the fiber of choice for many custom builds, racing cats, and Gunboat.
B. Mats, Strands, Roving, Direction, and Weights
Fibers are woven into matting and cloth for construction. Depending on the application, different weights of cloth and cloth patterns and weaves may be more appropriate for the job.
Cloth weight refers to the weight per square yard (or meter) of the cloth. A square yard of nine ounce cloth weighs nine ounces. The heavier the cloth, the stronger it is in a laminate.
Fibers carry loads along their length, so cloth weaves have directionality to their strength. Most builders use several layers of cloth with different orientations to give good universal strength to hulls. Specific FRP applications with strict load-path requirements may have more unidirectional fiber layering – for example, a chainplate manufactured from carbon fiber may use unidirectional fiber.
Cloth – fiberglass cloth is commonly used on outer layers of composites. Cloth may have unidirectional or bidirectional strength. Bidirectional cloths have maximum load strengths in two perpendicular directions. Variations on weaves like a modified twill allow a more flexible cloth for better shaping around complex molds.
Mat – is omnidirectional strands of fiber compressed into a cloth. This is often held together with a resin soluble glue, which makes mat great at conforming to mold shapes without folding and bunching as it collapses when wetted. Because the strands do not align, fiber strength is the same in all directions.

Woven Roving – a heavier cloth made from larger bundles of strands. Woven roving allows for quicker buildup of material and strand weight.
Most FRP layups include multiple layers of different cloth and mat. Finished layers may be finer cloth over courser cloth, over woven roving and mat.
Three primary resins are in common use in marine construction – polyester , vinylester , and epoxy . All resins have materials safety concerns and require care in their use and handling.
Polyester is the least expensive and requires breathing protection because of the VOC emission (Volatile Organic Compounds…nasty, smelly fumes). It doesn’t have good bonding/gluing capability, and should only be used with glass fibers for structural building. Some polyester resins are referred to as “isophthalic” resins.
Vinylester is chemically similar to a hybrid of polyester and epoxy, and performs best with fiberglass. It shouldn’t be used in high strength applications with carbon or aramid fibers. It has some adhesive qualities which polyester lacks, it shrinks less during curing, and has better impact resistance.
The added strength of vinylester coupled with increased water resistance makes it an attractive option for many catamaran builders. It costs less than epoxy, but still has better performance than polyester.
Epoxy is the most expensive, but is three times the strength of the others. It offers the best adhesion and the only resin for building structural elements with carbon and aramid. It resists water intrusion better than the other resins, resists blisters, emits no VOCs, and shrinks less. The major drawback is it is more brittle if it takes an impact.
While epoxy is “the best” in terms of strength and ease of building, there are many applications where other resins are appropriate. Budget is a big driver – a boat made from E-Glass doesn’t need epoxy resin, and considerable cost savings to meet a construction price target may drive the choice.
They can build quality boats from all material combinations, but price and performance will drive materials choices to keep some boats more affordable.
2. Cored Construction
What’s the best way to make fiberglass strong? To a point, you can make it thicker. As it gets thicker, it gets heavier. A hollow shape can take more compressive load than a solid one of the same weight, and the same principle applies to fiberglass construction.
Consider an I-Beam used in building construction. It has the same strength (or more) as a solid rectangular beam of similar mass. The compressive load on the beam is supported by the outside edges of the material, the metal in the middle doesn’t contribute much to the strength. So we can remove metal to get the “I” shape while still keeping those sides rigid, making a lighter girder with less material.
The same principle applies to cored construction with fiberglass. Making a sandwich of two layers of fiberglass with a light core between them allows for the greater strength with weight savings.
There are drawbacks – the biggest risk is damage which breaks the skin, which can let water into the core. Earlier cored construction used materials prone to saturation and rot if they got wet. Some builders opt to do cored construction above the waterline and solid below to minimize some of these risks.
But the advantages in weight savings and increased stiffness offset the drawbacks, and there may be a few other side effects like sound and temperature insulation. Like resins and fibers, core materials offer distinct advantages, disadvantages and price points.
Most builders have adopted a hybrid approach, building solid hulls below the waterline, and cored hulls and decks above. This gives a balance of weight and safety.
A. Balsa Core
Balsa is light and inexpensive. The first cored construction used balsa, but it has the disadvantage of being wood. As a natural material, if it gets wet it can rot and break down. Builders use “end grain” balsa – shorter cross cut sections – to prevent wicking of water if there is an intrusion.

B. Foam Core
Closed cell foam cores give good strength to weight savings while minimizing water intrusion. If you get water in the core, it won’t spread very far. Divinycell is a popular PVC foam core, though there are several choices with different densities and compressive strengths.

Some foam cores are not suitable for heat treatment, but infused or vacuum bagged boats like the Outremer and PDQ do well with it.
C. Honeycomb
Honeycomb cores are often the most expensive, but also give some of the best strength to weight ratios. Honeycombed cells made from resin cured aramid papers are some of the best, but also among the most costly. They offer good stiffness, but can be hard to shape. Aluminum and other resin-infused papers are other core materials builders can choose from.
3. Construction and Resin
When building a hull, there are optimal ratios of fiber to resin saturation for target strength and weight. Too little resin and you may not have enough strength (or worse, voids and gaps), and too much, and you’re just adding weight without adding strength. Resins are also a significant material cost in building the boat, so over application not only increases weight but adds cost.

There are many ways to assemble the cores, fibers and resins to build a finished laminate hull – we’re addressing the most common in boat building. Each approach has strengths and limitations, and an impact on the bottom-line cost to build the boat. Any voids or air pockets in the laminate can be disastrous; these techniques have been developed to increase saturation and reduce the risk of voids.
A. Hand Layup / Open Molding
As the name implies, this is the application of resin by hand to cloth as it’s laid into a mold. Wetting is done with a brush, and the laminate is rolled out to remove any air pockets and voids. This is the simplest way to lay up fiberglass, but also the least precise and consistent and will use the most resin.
Skilled craftsmen have built some of the finest vessels in the world this way. Though it’s more popular with monohulls, which are less sensitive to weight, many catamarans built with hand layups on open molds are still out cruising and performing well.
B. Spraying
Using chopped-strand fiber mixed with resin, a “chopper gun” can spray the mixture into a mold to lay down the composite. A consistent thickness can be difficult, but this is a low cost construction technique which makes a very resin-rich laminate. Using sprayed fibers gives lower strength in all directions compared to meticulously laid down mat and bi-directional cloth. But it is a quick technique popular with mass produced, smaller boats.
It is an excellent technique for parts with complex geometry where weight is not an issue, but you will not see it often in catamaran construction. It’s heavy with resin without any resultant increase in strength.
C. Vacuum Bagging (Wet layup)
When an open molded component has been laid up and wetted with resin, vacuum bagging takes the process a step further. After the wetting is complete, air tight plastic bagging is secured around the wetted area, and the air is pumped out of the bag. The vacuum pulls excess resin out and collapses air pockets.

The goal is to get thorough wetting and produce as strong a laminate as possible without excess resin. Knysa and Leopard are two builders that use vacuum bagging on their hulls to reduce weight.
D. Resin Infusion
For resin infusion the cloth, matting and core is laid in place dry, then sealed in an air-tight bag. A vacuum pump attaches to one side of the bag, and on the other a feed for resin. The vacuum sucks the air out of the dry cloth stack, then pulls the resin through the stack, infusing and wetting it.
Resin infusion, when done right, gives the lightest, strongest laminates with no voids and the minimum resin weight for maximum strength. SCRIMP is a variant of the resin infusion process used by some builders, including TPI which build many early Lagoon cats.
E. Pre-preg
Using pre-preg (for “Pre Impregnated”) cloth for your laminating gets rid of the resin bucket. They manufacture cloth with a partially catalyzed resin pressed into it, then it’s chilled or frozen to stop the curing process. There is no need for seperately mixed resins, and there’s no worry your resin might “go off” and harden before you’re done wetting the cloth. Instead, the cloth is assembled, vacuumed, then heated to kick off the curing process.
There are both advantages and disadvantages to using pre-preg for your laminate work. The big disadvantage is the cost; it is most expensive material to use. You also need to chill and store the cloth until you need it, though some can be at room temperature for a couple of weeks without kicking off. And you need an oven which requires some clever tricks if you’re building a forty or fifty foot boat.
But the strength to weight ratio will always be perfect. High tech honeycomb cores are best suited to pre-preg lamination, and without racing against resin cure times, you can ensure perfect cloth placement and precise layout in the build process.
The primary use for pre-preg in boating is high performance race boats. With catamarans, pre-preg may be used high load parts, like Gunboat does for foils and rudders.

4. Industry Examples
Across the catamaran building industry you’ll find almost all the above techniques and materials used, though some are less common. You aren’t likely to find chopped strand sprayed layups in ocean going cats, and hand layups can lead to heavier hulls than weight sensitive catamaran designers prefer. Most manufacturers have moved to vacuum bagging or resin infusion, with a few of the highest end boats using pre-preg for key components.
Built by Robertson & Caine in South Africa, the hull material is vacuum bagged, end-grain balsa-cored E-glass with polyester.
Hand laid, bagged vinylester over an Airex foam core in the hulls.
Earlier Prout catamarans like the Snowgoose 34 featured hand laid solid FRP hulls and decks. Over time they switched to foam or balsa cores for decks and above the waterline.
Older PDQ boats were made from vacuum bagged vinylester – solid below the waterline and cored with CoreCell foam above the waterline and in decks. Newer PDQ models switched to epoxy resin.
All glass is vacuum bagged. Below the waterline is solid E-glass and vinylester. The rest is unidirectional, bidirectional, and triaxial cloths over a Nida-Core polypropylene honeycomb core with isophthalic and vinylester resins.
The Gemini cats are built with a solid hand layup of woven roving and fiberglass mat and polyester resin. Decks are cored with end grain balsa. The Gemini 3200 introduced vinylester resin into the layup to prevent blistering.
Older Lagoons were SCRIMP infused vinylester with and end grain balsa core above the waterline and in the decks.
Newer Lagoon catamarans use polyester and vinylester resins, also infused with balsa cores above the waterline and solid below.
With a carbon fiber inner skin, Catana also uses Twaron aramid fibers in the sandwiched hull over a foam core.
Fontaine Pajot
Primary hull construction is resin-infused vinylester with a balsa cored hull and deck.
Beneath the waterline, Outremer uses a single layer, solid vinylester laminate for safety. The hulls and deck are vinylester with a Divinycell foam core. They stiffen certain components with carbon for rigidity and durability.
Gunboat hulls are epoxy infused carbon fiber with a Nomex honeycomb core. They build dagger boards and other high load components with pre-preg carbon.
- Tags Buying Advice

By BJ Porter
Owner of Hallberg Rassy 53; world explorer.
4 replies on “Catamaran Construction – Hulls, Laminates, and Composites”
Excelent. Thank you for this I learned allot. Johan
Very straight forward information. Thankyou for doing this.
Damn…What an Amazingly Informative Article. *Cheers*
Outremer publish on their website that they use polyester. Not vinyl ester as you have stated.
Leave a Reply Cancel reply
Your email address will not be published. Required fields are marked *
Save my name, email, and website in this browser for the next time I comment.
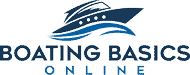
Boating Basics Online is reader-supported. When you buy via our links, we may earn a commission at no cost to you. Learn more
How to Build a Fiberglass Boat? – Find Out All Easy Steps
Written by J. Harvey / Fact checked by S. Numbers
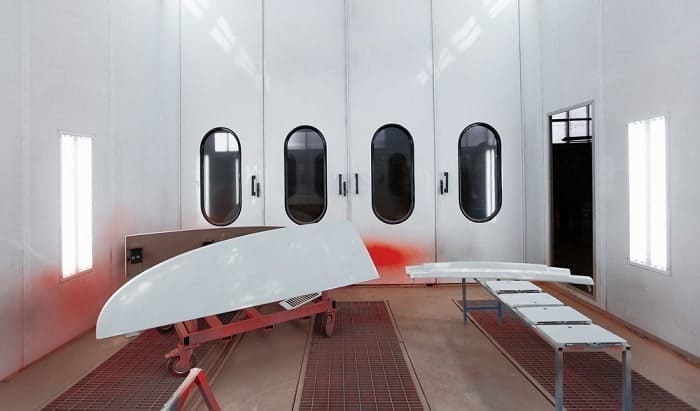
People have used materials such as wood, concrete, bamboo, paper, and leather throughout millennia. But the most renowned contemporary material among the long list of boatbuilding materials is fiberglass.
The exact material that you need in how to build a fiberglass boat construction is glass-reinforced plastic or fiberglass-reinforced plastic. It has a binding nature when mingling with fibrous material. This kind of fiberglass can be stiffened and become solid.
To make a fiberglass boat, you have to prepare a mold for it due to its size. More details will follow for you to finish one. You’re in luck as this article will guide you all the way!
Table of Contents
Step 1. Starting with a Mold
Step 2. dry fitting, step 3. filling the holes with epoxy, step 4. wrapping the boat with fiberglass, step 5. flood coating on fairing filler, step 6. painting your boat, processes to build a fiberglass boat.

A mold is simply the foundation of a DIY fiberglass boat. You may use plywood and some pieces of wood for this. A prefabricated jig to form a hull is essential in this part. The wood is referred to as veneers, and you can glue them together with epoxy resin.
Clear Table Top Epoxy, ProMarine Supplies Art Resin, and Better Boat Epoxy Resin Crystal Clear are dependable marine epoxy resins. The inside and outside of fiberglass are strengthened and protected all at the same time by this substance.
You can make the mold based on the size and shape that you prefer. There are two kinds of mold that are labeled as male and female. Marine fabric is needed in both methods.
Opting for a male mold would require you to lay over the fiberglass on its exterior surface. The catalyzed liquid resin is essential when the fiberglass goes through saturation.
With this method, the build-up of lamination will happen inside out. Take note that the outermost layer is the last thing to work on. Polishing the outer layer will give you a nice and shiny surface.
- Female Mold
When it comes to female mold, the outermost layer comes first. You can polish the working surface, so you’ll get the shiny finish when the fiberglass is added. In this method, you have to place the fabric on the mold’s interior before wetting it out.
Although there are two kinds of molds, complex hull shapes can be created out of fiberglass. But some shapes are easier than others. Also, don’t forget to inspect all the parts of your mold for any existing flaws.
For instance, you can find a bottom that is a little wavy. You can do some pushing or pulling to make the surface smooth and flat. Some may need to pull thickened epoxy inserted in the middle of zip ties.
It’s uncomplicated to remove the weight once the epoxy is dried. Cut the zip ties to get ready for fiberglass application.
Dry fitting the fiberglass starts with sanding the boat’s sides and bottom. Leave a ¼ radius on the edges for trouble-free wrapping of fiberglass. The fiberglass should be cut into six inches longer than the shear.
You also need a half-inch or an inch allowance for the widest dimension when cutting the fiberglass. The front side of the fiberglass is usually longer, so trimming is necessary. Using a sharpie and scissors will make things easier.
Be careful when working and avoid abrading or pulling the fiberglass apart. Trimming the hanging excess can be done when curing time is over.
There will be holes that you have to cover due to the plywood’s seam and zip ties. They must be filled before placing the fiberglass on the mold. So, spare yourself from having additional work like sanding by doing the fillings properly.
Of course, you can let the epoxy dry first then sand it before laying down the fiberglass. Use an old shopping card and mix the thickened epoxy. Next, pull it through in exchange for filling the holes.
Some epoxy may go through, and cleaning the other side is needed after flipping the boat over. There’s nothing to worry about as all holes and even cracks in the boat are packed with resin.
Continue using epoxy to cover the whole boat by using a foam roller or chip brush. It’s a preparation for setting down the fiberglass.
After applying epoxy to the whole boat, you can carry on with fiberglass application. It’s best to begin on the sides when building fiberglass boats. You’ll see that it sits in a loose position, but whatsoever, you can get back to some areas for fixing to achieve the shape and appearance that you like.
When you finish putting the fiberglass, you’ll find wet areas and some that are not. But you can get a roller or brush to start applying the resin. At this point, all the necessary applications are done. Give it time to become tacky.
You can give it an hour or up to 3 hours. The amount of necessary time varies as it affects the temperature. The curing time becomes quicker when you’re working under high temperatures.
In this step, you have to mix epoxy and microlight fairing filler to have the flood coating. The benefit that you can gain from it is you only sand the resin but not including the fiberglass. Just lightly brush the entire hull with the help of a chip brush.
Once this process is done, the fiberglass is also cured. Hence, you can trim the edges and sand them for smoothness. But be attentive not to sand the fiberglass. You can roll the boat over to apply the fiberglass in the interior part.
You still need to add epoxy first, even at the seams, just like what you did with the exterior part. Then you can add the fiberglass. As you can see, these steps are for female mold, which is commonly used.
But nothing is too different when you go for a male mold as you only need to do the steps the other way around. You’ll need to start working on its interior part.
When you build a fiberglass boat at home, you have the chance to customize it. However, you may start by using a primer that is two-part-based epoxy. Clean and rinse the newly made boat, then let it dry before you can apply the primer.
Use 36-grit sandpaper to prepare your boat for painting. If you don’t want to use a primer, you may use Xylol instead. You can use any type of paint, but the best option is the two-part polyurethane due to gloss retention and durability. Protect the painted hull while it’s being dried from tiny particles and bugs.
It may take time and effort when you commit to a DIY project. Learning how to build a fiberglass boat is an example. But it’s worth it as you’ll be able to form any hull shape out of fiberglass.
Fiberglass boats are common nowadays, and choosing this material is not just jumping on the bandwagon. Most boaters depend on it as it’s tough and easy to repair with more advantages as it has low cost and maintenance. So I hope this article has helped you out; and if you find this article useful, feel free to share it to those who may need this.
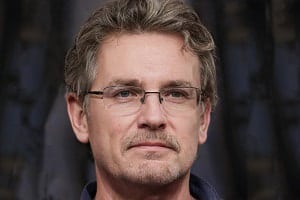
“I am James Harvey – founder of Boating Basics Online. It is established with the drive to help out first-time boaters, which are those desiring to explore their way through the water. So if you are new to boating, start from here with me. “
- See the full showroom
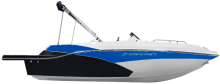
Starting at $32,300
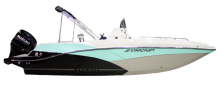
Starting at $32,299
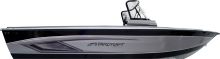
Starting at $60,882
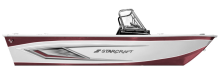
Starting at $55,821
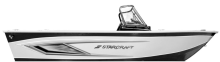
Superfisherman
Starting at $46,494
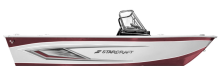
Starting at $39,482
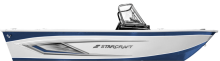
Starting at $29,225
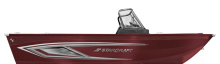
Starting at $25,662
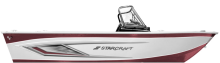
Starting at $23,442
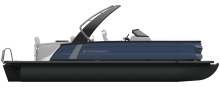
Starting at $100
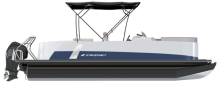
Starting at $90
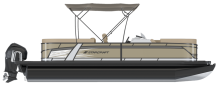
Starting at $80
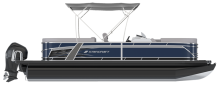
Starting at $70
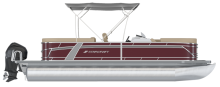
Starting at $60
Starting at $50
Starting at $40
Starting at $30
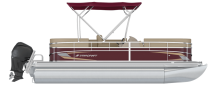
Starting at $20
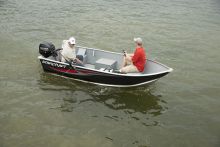
Fiberglass Construction
Every detail sets us apart. .
Starcraft fiberglass boats are constructed to the most exacting standards. Learn more about the elements that add up to industry-leading quality.
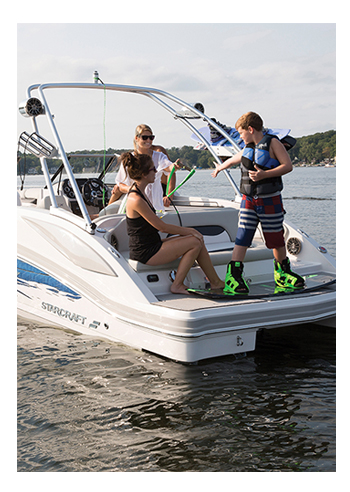
- We start by applying wax to our meticulously cared for hull and deck molds. 22 ml of ISO-NPG high luster Gel Coat is applied followed by a Blister-Guard barrier coat to protect the appearance of your boat.
- An integrated stringer system provides unmatched strength and durability.
- Alternating layers of 24 oz. woven roving and 60 ml fiberglass matting fully encapsulate all stringer components.
- An 8-inch overlap is made at the hull bottom to ensure the boat is the strongest where it needs to be.
- Each deck contains 2 ml of coremat and 18 oz. of bi-axial fiberglass for the best possible quality.
- Each hull is weighed for consistency and thoroughly inspected before it moves on to the assembly process.
- All unfinished surfaces are coated with Gator Shield protective coating that is anti-shock, reduces noise and protects against rust and water intrusion.
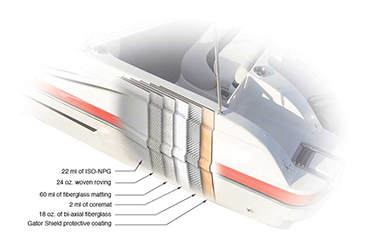
DRIVER'S CONSOLE : Luxuriously appointed helm station with ergonomically designed dash and helm seat.
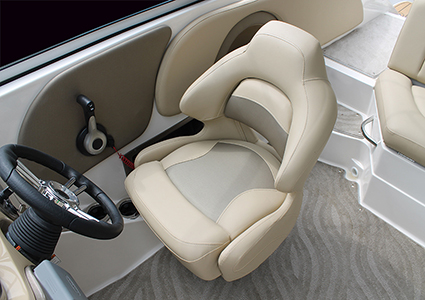
35 OZ. VINYL UPHOLSTERY: Comfortable and strong, the upholstery features self-draining foam for lasting durability.
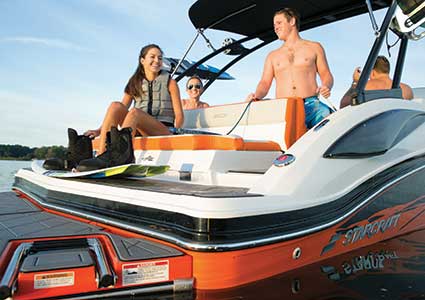
SURE STEP SAFETY PLATFORMS: Wide, secure swim platforms, both front and aft, feature deepwater ladders for safety and convenience.

UNITIZED 2-PIECE HULL: Top and hull are screwed and bonded together, creating the added strength needed to secure your lifetime hull warranty.
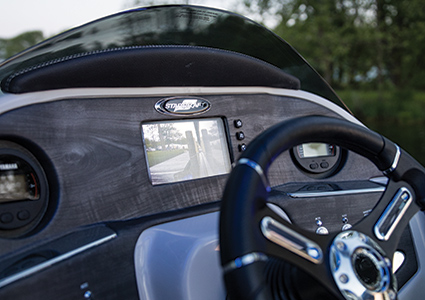
BIGGIE VISION CAMERA SYSTEM: Our exclusive rear camera system enhances safety by providing a view of activity behind the boat during swimming and watersports and eliminating blind spots while docking.
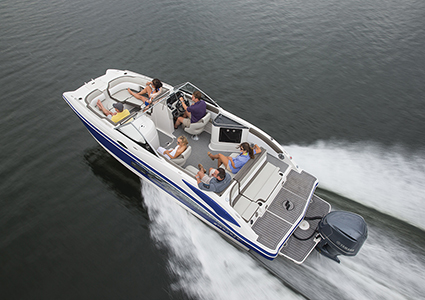
SPACIOUS INTERIORS : Starcraft leads the way with innovative floorplans that maximize space inside the boat. From the roomy walk-in bow with seating for 4, to the added safety and comfort of deep interiors, to plush, generous bucket helm chairs — it's all about being able to spread out and enjoy the day.
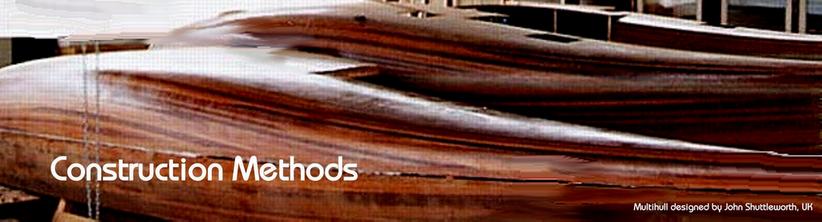
C‑Flex fiberglass planking (for 'one‑offs' over a male mold)
C‑Flex® is a type of fibreglass 'planking' that was created by and is still sold by Seeman Composite Inc. since the 1970s. It's made up by using continuous, flattened longitudinal glass rods with roving in between, and it's all woven together with a light fiberglass cloth to keep things in position, and this allows it to be worked on the bias to create compound surfaces.

Typically, it is stapled over a male framework of wood station templates and only after being in place, is the resin rolled on. Typically, a casting (mold) resin is used, as this shrinks far less.
The 'planks' can be cut with tin snips or when bunched together, with a fine metal saw. The CF‑39 plank needs a transverse frame not farther than 14" apart and 12" is recommended as this can reduce the fairing later on. The outer edge of the 'planking' is stapled while dry to the temporary frames, typical with small stainless or monel staples about 3 ⁄ 8 " long with a small ( 3 ⁄ 16 ") crown.

A small boat like this would typically have only need one layer of C‑flex planking, though a light mat with woven roving would be added to the interior to complete the skin, after the boat was turned over and the temporary frames removed. The use of C‑flex will nearly always benefit from a more elaborate mold, as the more support the soft material has, the less fairing will be required later. The comment 'C‑flex can require extensive fairing' is one of the things that has been levelled against the product in the past. One of the more consistent supporters of C‑flex over the years has been the fine designer Bruce Roberts from 'down under'—though he works primarily with monohulls. Here is a sketch from his on‑line data, showing longitudinal battens first laid over the station templates and then overwrapped with wide flat battens (glass or wood) from sheer to keel, to provide much more support to the dry C‑flex than would just the templates alone. This method also permits easy fairing of the exterior surface with shims etc, in the event that the stations are not computer generated and perfect.
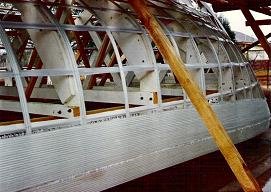
By using a milled fiber paste (~75% resin) instead of the normally specified chopped strand mat required between the C‑flex and woven rovings, Seeman Composites claim that the weight of the mat portion of the laminate can be cut by 50%. That's still a relatively small part of the total laminate though. More specific information is available from the Seeman Manual at this site: seemanncomposites.com/CFLEX20MANUAL-WEB.pdf
- Probably the only proven method to build a one‑off hull in solid glass+resin (FRP).
- Creates a boat with high longitudinal strength, as the fibreglass 'rods' in C‑flex are not only relatively large and solid compared to all other glass fibres but they are also laid in as one piece from bow to stern.
- C‑flex lays on as multiple lengthwise battens and therefore provides basically fair lines over the construction form.
- The cloth that binds the solid 'rods' permits a lot of flexibility to follow compound hull shape and the 'planking' can be spread or compressed a little to fit.
- C‑flex can be totally laid on dry and positioned easily and rapidly with simply a staple gun.
- By stapling down each rod to the mold, the material can be made to lie in concave areas and therefore works for boats that have a flare.
- A solid hulled boat is going to be relatively heavy by today's standards and even though C‑flex is no heavier than a custom built solid fibreglass hull (and arguably lighter for the same strength), its weight must be considered a disadvantage compared to other, perhaps less rugged methods.

- A solid glass boat is not only heavy but will also require added interior insulation to avoid condensation. Many of the alternative systems will not have the same issue and also have a better natural finish for the interior.
* This 'dipping', while caused slightly by resin weight on horizontal surfaces, is principally from resin shrinkage on curing. This has the effect of pulling a curved surface somewhat straight between supports, then requiring more filling to make the hull surface fair. For this reason, only low‑shrinkage molding (casting) resins should be used for the critical first layer of C‑flex. There is a slight premium a pay for this but little option. Even then, expect a slight tightening of the C‑flex and the justification for using closer supports than normal.
"New articles, comments and references will be added periodically as new questions are answered and other info comes in relative to this subject, so you're invited to revisit and participate." —webmaster
"See the Copyright Information & Legal Disclaimer page for copyright info and use of ANY part of this text or article"
.png)
Excellence Through Innovation
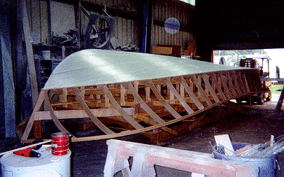
IMAGES
VIDEO
COMMENTS
With fiberglass boat building, however, the major components of the boat - the hull, deck, liner, and large parts like consoles—are molded from fiberglass. Usually, this means starting with a female mold. The mold is first sprayed with gelcoat, then fiberglass cloth is applied, and then resin is used to saturate or "wet out" the fiberglass.
Layers of gelcoat are sprayed onto the mold to form the outer layer of each hull. Each hull is then laid up with a precise number of layers of fiberglass, resin, and various core materials that are all placed in each mold by hand. Dufour Yachts. The hull is beginning to take shape as the layers of fiberglass and resin are applied to the hull mold.
Bonadeo uses the resin-infusion technique for his hulls and larger parts where all the laminates are laid out dry, bagged and put under vacuum. The resin is then pulled through the fiberglass and other laminates like Kevlar and carbon fiber. "This process gives the laminate a better resin-to-cloth ratio," said Bonadeo.
Fiberglass boat construction became popular in the 1960s and today is perhaps the most common way production boats are built. Upsides to this method include relatively low maintenance, high strength, ease of repair, and generally low cost when compared to other boatbuilding materials. Primary downsides are osmotic blistering in some hulls and ...
On average, a 20-25-foot boat hull made of fiberglass can cost anywhere from $5,000 to $10,000 or more, Pros and Cons of fiberglass. Fiberglass is a popular boat-building material for good reason, but it's not without its drawbacks. Let's take a look at some of the pros and cons of using fiberglass in boat construction. Pros
Fiberglass Composite Construction. The fiberglass composite boat building process involves placing composite materials between layers of fiberglass. It creates a very strong hull that is lighter than an all-fiberglass boat. Using a jig, the sheets, panels and strips of composite foam are glued together to form the hull.
Beyond Glass Fiber. Carbon fibers and aramid fibers are lighter than glass fibers and, in many configurations, stiffer and stronger too. But they don't come cheap. Today, glass fiber may cost between $1.50 and $2.50 per pound, while carbon fibers may run in the pricier $18 to $26 per pound range.
Every Westport yacht features proven technology in composite construction. Westport exclusively builds all hulls and major deck parts in one-piece, precision-engineered molds. Fewer parts mean greater structural integrity and resistance to stress. For the Westport yacht owner, that translates to year after year of enjoyable, trouble-free cruising.
First, mark the desired location of the deck or cabin on the hull of the boat. Then, using a drill, create holes for mounting screws. Next, position the deck or cabin in place and screw it into the hull. Finally, seal any gaps with silicone caulk to ensure a watertight seal.
Since 1959, when Hatteras Yachts Founder Willis Slane launched the first boat under 30 feet built of fiberglass rather than wood with the goal of conquering the stormy seas off the North Carolina coast, we've been at the leading edge of advanced hull construction. "I love the product we build, and that it's known throughout the industry ...
Cast Nets We Use → https://bit.ly/2X9EJJjCast Net Mastery Book → https://amzn.to/3k9wfL7Join ReelReports → https://www.reelreports.comIn today's episode of...
Fiber choices in the last few decades have expanded past the glass fibers used in the first mass produced boats in the 1960s. FRP construction wasn't new even then, they built the first composite boats using modern fiberglass in the 1940s. The major fibers used in marine construction fall into three categories - glass, aramids, and carbon.
Epoxy is often used when making repairs to fiberglass boats and may be used in the secondary phase of construction when structural parts are being attached to an already cured hull. Epoxy is also often applied below the waterline as a barrier coat to prevent blistering. But because it is so very expensive, it is rarely used as the primary resin ...
How is a fiberglass boat made? Great question and it is different than a lot of people think. We show you a step by step process and give you detail so you u...
Step 1. Starting with a Mold. A mold is simply the foundation of a DIY fiberglass boat. You may use plywood and some pieces of wood for this. A prefabricated jig to form a hull is essential in this part. The wood is referred to as veneers, and you can glue them together with epoxy resin.
Every Detail Sets Us Apart. Starcraft fiberglass boats are constructed to the most exacting standards. Learn more about the elements that add up to industry-leading quality. We start by applying wax to our meticulously cared for hull and deck molds. 22 ml of ISO-NPG high luster Gel Coat is applied followed by a Blister-Guard barrier coat to ...
A description of the C-Flex material and its use in the construction of one-off boats. ... C‑Flex fiberglass planking (for 'one‑offs' over a male mold) C‑Flex® is a type of fibreglass 'planking' that was created by and is still sold by Seeman Composite Inc. since the 1970s. It's made up by using continuous, flattened longitudinal glass ...
C-Flex is a unidirectional fiberglass building material originally developed for the manufacturing of custom boats. Since its invention, countless structures, marine and otherwise, of all shapes, sizes and complexity have been affordably built using this simple construction method. The design of C-Flex allows any form to be built using simple ...
A Detailed Analysis. The typical range for fiberglass boat hull thickness is 10-20mm. Factors like boat hull design and construction methods influence hull thickness. Innovations in boat hull construction have made the boats safer and more efficient. Unlock the mystery of fiberglass boat hull thickness.
Thousands of boats were under construction on the West Coast and old wooden boats were being demolished by the hundreds of thousands worldwide. Beautiful bronze parts were available. Fiber glass materials were relatively inexpensive and distressed sales were all over the place. I heard that 10,000 ferro cement boats were built on the West Coast.
Fiberglass Boat Design and Construction. by Robert J. Scott (1996) This book presents the small boat designer and builder with a basic insight into the nature of fiberglass as a boatbuilding material, as well as a sound, yet simple, approach to analyzing fiberglass boat hull structures. A thorough review is given to the characteristics of ...
4) Streamlined Construction Process: The construction process using bulkheads and sandwich panels follows a streamlined approach. It begins with the installation of bulkheads at strategic positions along the boat's length. These bulkheads serve as the framework for shaping the hull and provide a guide for the subsequent construction steps.
Fiberglass Fabrics & Tape Paint & Varnish Sealant, Filler, etc. ... Every year, thousands of amateurs much like yourself build their own boats the proven Glen-L way. Many builders save 50% or more over the price of a factory-built boat. ... Non-Boat Designs; Alternative Construction; All plans come with a 30-Day money back guarantee.
Moran Yacht & Ship is proud to be considered one of the world's best yacht companies; a leader in luxury yacht sales, construction, charter, and management. Whether you are interested in buying a yacht, selling your yacht, luxury yacht charter, or new yacht construction, our super yacht brokers and yacht managers are here to assist.